Quality management
Optical quality control through high performance camerasHigh quality products are the foundations of every business. In correlation with economic aspects, they define a company’s attractiveness for the customer. It is therefore our declared intention to continue uniting both aspects in the best possible way.
Our quality management system is orientated towards the requirements of the automobile industry and is set up in accordance with DIN EN ISO 9001 and IATF 16949. Furthermore, the use of modern quality management methods such as SPC, FMEA or Six Sigma ensure a consistently high quality. Above and beyond the purely formal criteria, we have embedded an awareness of quality in our company culture. We have therefore developed specifications based on concrete questions and compliance is ensured by every employee in their respective work.
All production processes, services and commercial processes are subject to certain quality requirements. We pursue a “zero error strategy” in the production design, prices, service and compliance with delivery dates. This means that errors should be identified at the root and be avoided, so that we are always capable of delivering fault-free products on time and in the ordered quantity. Whether this internally defined standard is implemented can principally be determined by the number and type of complaints. These are reflected in the notices regularly published for each product area individually, as well as for all product areas. Every employee can use this as a basis to see the areas where there is potential for improvement and where changes can be made directly on location. The means that everyone in our company can make their own contribution towards avoiding the cost of errors and helping to maintain our competitiveness.
Contact us
We help you furtherDo you have any questions, requests or suggestions? Then we look forward to hearing from you and will be happy to get in touch with you as soon as possible.
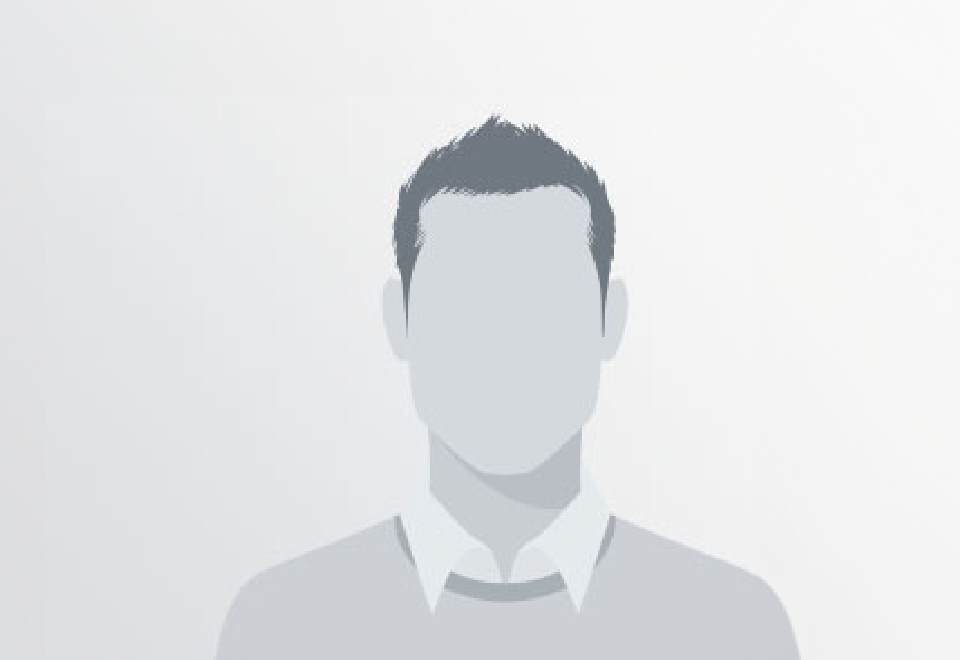